Extreme heat exchanger using metal 3D printing
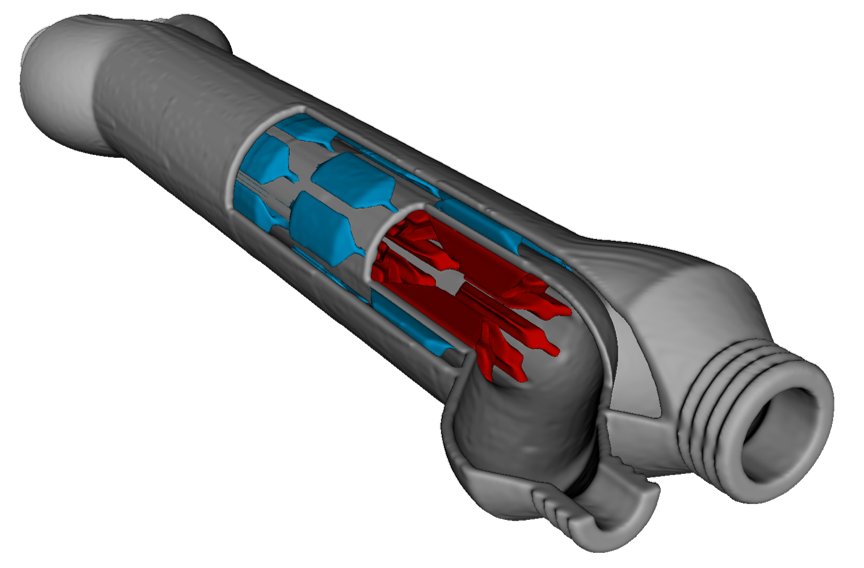
Ultra-power-dense heat exchanger development through genetic algorithm design and additive manufacturing
has been accepted to Joule.
- We use shape optimization to design an ultra-compact heat exchanger
- We manufacture the devices using metal additive manufacturing from AlSi10Mg
- Thermal-hydraulic experiments demonstrate high heat transfer
- The device has 20× higher specific power than a comparable commercial device
Press Release
-By University of Illinois Urbana-Champaign
Demonstrating next-generation energy technology, researchers at the University of Illinois Urbana-Champaign are using topology optimization and metal 3D printing to design ultra-compact, high-power heat exchangers.
Used in most major industries - including energy, water, manufacturing, transportation, construction, electronic, chemical, petrochemical, agriculture and aerospace - heat exchangers transfer thermal energy from one medium to another.
For decades, heat exchanger designs have remained relatively unchanged. Recent advancements in 3D printing allow the production of three-dimensional exchanger designs previously thought impossible. These new and innovative designs operate significantly more effectively and efficiently but require specific software tools and design methods to manufacture the high-performance devices. Recognizing the need to unlock new, high-performing heat exchangers, Grainger College of Engineering researchers have developed software tools that enable new 3D heat exchanger designs. For further information see the IDTechEx report on 3D Printing Software 2018-2028: Technology and Market Analysis.
“We developed shape optimization software to design a high-performance heat exchanger,” said William King, professor of Mechanical Science and Engineering at The Grainger College of Engineering and co-study leader. “The software allows us to identity 3D designs that are significantly different and better than conventional designs.”
The team started by studying a type of exchanger known as a tube-in-tube heat exchanger - where one tube is nested inside another tube. Tube-in-tube heat exchangers are commonly used in drinking water and building energy systems. Using a combination of the shape optimization software and additive manufacturing, the researchers designed fins (only made possible using metal 3D printing) internal to the tubes.
“We designed, fabricated and tested an optimized tube-in-tube heat exchanger,” said Nenad Miljkovic, associate professor of Mechanical Science and Engineering and co-study leader. “Our optimized heat exchanger has about 20 times higher volumetric power density than a current state-of-the-art commercial tube-in-tube device.”
With billions of heat exchangers in use worldwide today and even more attention placed on our need to reduce fossil fuel consumption, compact and efficient heat exchangers are increasing in demand, particularly in industries where heat exchanger size and mass significantly impacts performance, range and costs.
Context
Heat exchangers are used in nearly every systems technology, including power generation, transportation, processing of oil and gas, building systems, water desalination, and electronics thermal management. The performance of heat exchangers is also a key component toward addressing the challenges of global sustainability. High performance heat exchangers typically use high surface area structures that promote the efficient flow of heat; however, the geometry of such structures is limited by their manufacturability as well as the software tools that guide their design. Here, we show design automation and additive manufacturing that can achieve high heat transfer with complex three-dimensional structures internal to the heat exchanger that cannot be made with conventional methods. The resulting device achieves a power density of 26.6 W/cm3 and a specific power of 15.7 kW/kg, which is significantly higher than that of most conventional heat exchangers.
Summary
This work presents the design, fabrication, and characterization of a three-dimensional heat exchanger (HX) having a tube-in-tube architecture using a genetic algorithm design and metal additive manufacturing (AM). The genetic algorithm aids the design of optimal fin geometries that minimize total thermal resistance between hot fluid and cold fluid. The genetic algorithm is coupled to a two-dimensional finite element method simulation to calculate conduction and convection in the device. Through careful thermal-hydraulic experiments, we demonstrate that our HX was able to achieve a power density of 26.6 W/cm3 and specific power of 15.7 kW/kg. The specific power of our additively manufactured device is 20X higher than that of a commercially available tube-in-tube HX with no fins. The optimized device also performs well compared with shell-and-tube and brazed plate heat exchangers that are designed for significantly higher heat transfer.
ASME News 3D Printing Progress 3D Printing Industry UIUC Press Release